Innovative power in the European paper sack and sack kraft paper industry
Constantly improving and innovating products, materials and processes has a long tradition in the sack kraft paper and paper sack industry. In 2022, the European sack kraft paper and paper sack industry celebrates a combined 160 years of innovative power! CEPI Eurokraft, formerly named Scankraft, was formed 90 years ago, in 1932. 20 years later, in 1952, EUROSAC was founded. Since then, the industry has not only grown in terms of members, numbers and areas of activity, but has also initiated many innovations that have improved and accelerated the production of sack kraft paper and paper sacks and enhanced product protection greatly. This timeline presents the major achievements of our vibrant history.
Note: In the timeline we do not pretend to be exhaustive, we have only made a short selection of interesting developments and innovations over the years.
A press release also summarizes the industry's milestones.
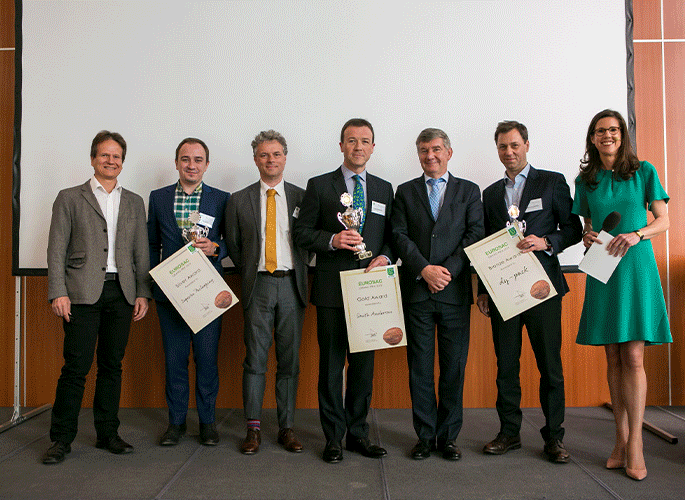
Today, EUROSAC represents over 75% of European paper sack manufacturers. Its members operate in 20 different countries. They produce more than 5 billion paper sacks per year, representing 650,000 tonnes of paper converted in 60 plants. Sack manufacturers from all continents and bag manufacturers contribute to the federation as corresponding members, and more than 20 suppliers (paper, film, machine or glue manufacturers) are registered as associate members. CEPI Eurokraft has also grown successfully. It now has nine member companies representing a volume of 3.0 million tonnes of paper produced. Together, their target is to develop 100% natural packaging solutions that meet the requirements of modern packaging, conserve natural resources and protect the environment for future generations as well as our own.
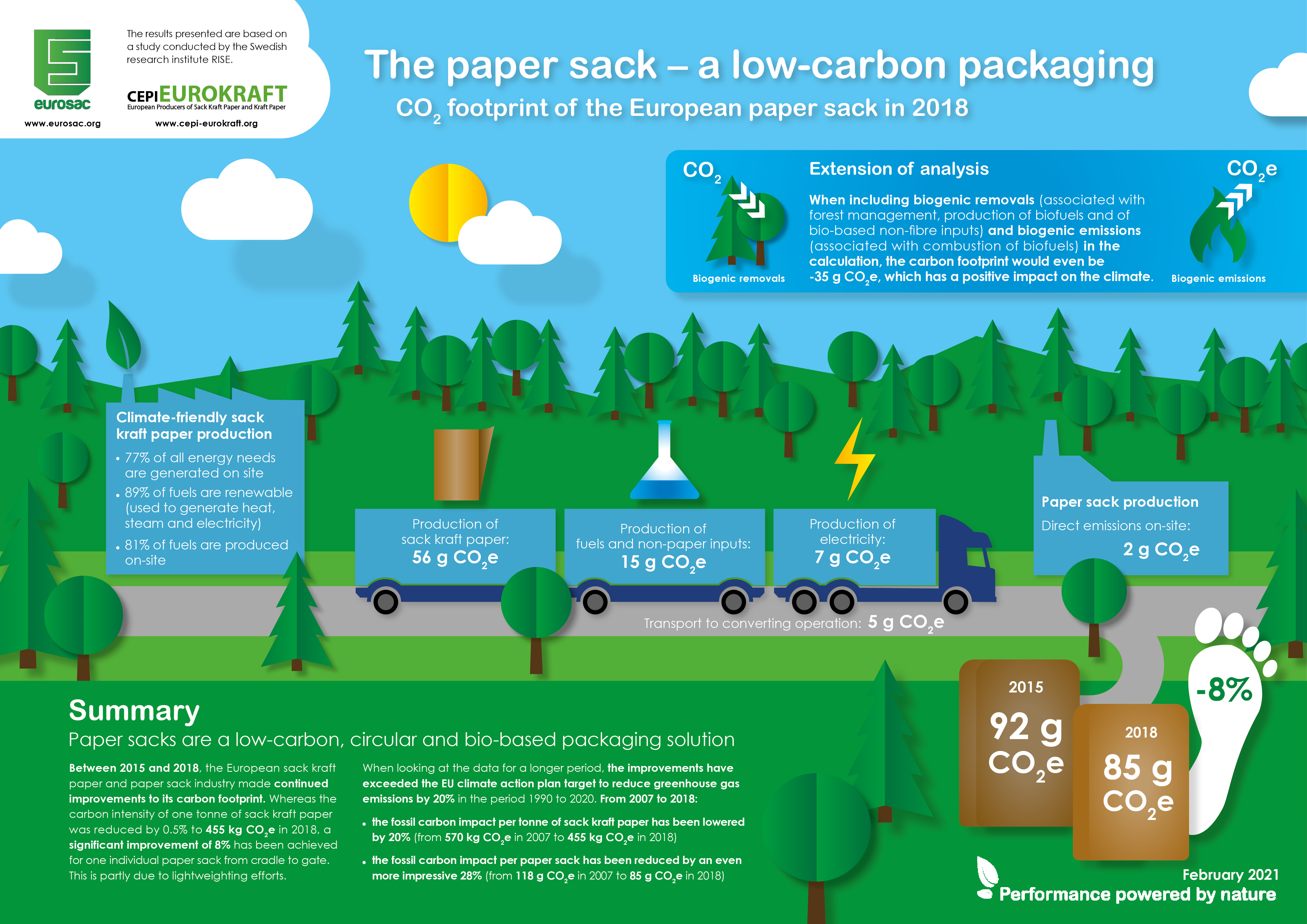
The kraft paper industry and paper sack industry is working hard to continuously improve its energy efficiency and increase the share of renewable energy resources. In 2018, the production of sack kraft paper is, to a high degree, energy self-sufficient: 77% of all energy needs (heat and electricity) are generated on-site. Adding to that, the production uses a high degree of renewable energy sources: 89% of the fuels are renewable and used to generate heat, steam and electricity. Most of them, that is 81%, are produced as side streams of the pulp and papermaking process. This achievement is made possible by continuous modernisation efforts. Two examples are a new heat recovery plant which was introduced by Nordic Paper in 1998–1999 that dries the paper with recycled steam instead of self-produced, and a biomass-fired boiler used by Gascogne since 2016. It replaces heavy fuel for the production of steam with renewable natural energy and reduces emissions by 40,000 t/year of CO2 equivalent, which equals the emissions of about 20,000 vehicles per year.
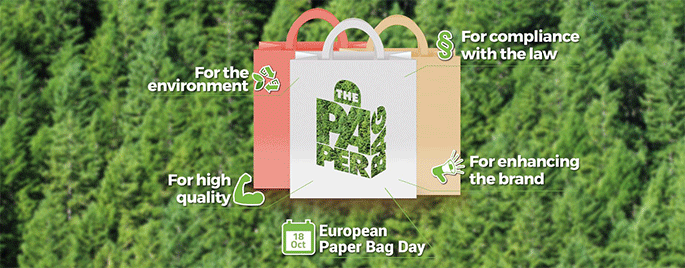
The Paper Bag platform is launched in 2017 by the leading European kraft paper manufacturers and producers of paper bags. They commit themselves to promoting the environmental credentials of paper carrier bags and support retailers in their packaging decisions to foster a worldwide bio-based economy. In 2018, they celebrate the first European Paper Bag Day. The annual action day takes place on 18 October every year and aims to raise awareness among consumers about paper carrier bags as sustainable and efficient packaging that contributes to fighting climate change and environmental pollution.
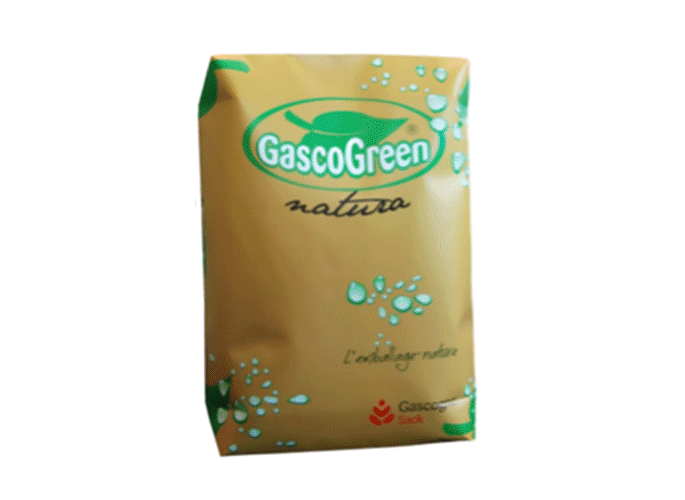
Around 2010, polyethylene barriers in paper sacks start to be replaced by bio-barriers, e.g. made from sugar cane, corn or cellulose. The earliest example is Terra Bag by Mondi. Introduced in 2010, it is the first industrial valve sack with a biodegradable free film for better humidity protection and with certified compostability. In 2014, Gascogne develops a biofilm sack (GascoGreen) with an inner film made using biodegradable and renewable materials that can be recycled and composted in industrial facilities. In 2021, three 100% plastic-free sacks offering moisture protection are presented at the EUROSAC Grand Prix Award. dy-pack develops gardyan, a paper sack for potting soil that masters the challenge of packing soil with a moisture content of more than 50%. MoistShield® by Fiorini is a special patented waterproof treatment which gives hydrophobic properties to any sack. ECO Layer by Klabin uses a resinous paper with aqueous dispersion of polymers with additives.
With the research into bio-barriers, the proportion of renewable materials in paper sacks is expected to increase in the upcoming years. The industry’s target is to produce 100% natural paper sacks.
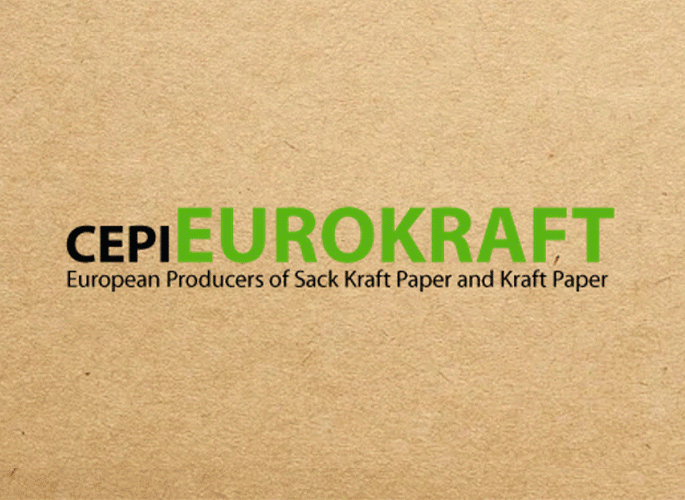
In 2000, Scankraft decides to become an association for all European kraft paper producers. To stress the affiliation to the European paper industry, the new association is organised as a CEPI industry sector under the present name CEPI Eurokraft. Its statutes are mostly a copy of the Scankraft statutes with some additions. All European kraft paper producers are invited to join.
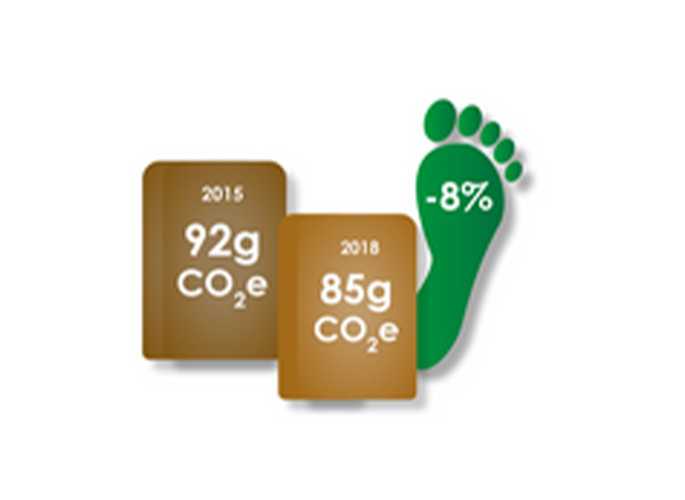
EUROSAC and Scankraft, now CEPI Eurokraft, combine forces in 1993 for their research, communication and political activities by creating the ESPACE Programme (Environmental Strategy Programme and Communication EUROSAC/CEPI Eurokraft). It is the starting point for many valuable studies, guidelines and communication materials for the industry. One example from 1993 is their first LCA study of average European sack kraft paper and paper sacks. It shows the early commitment to and strong focus of the industry on sustainability in its production processes. Looking back, the results of the regularly conducted study show a consistent downward trend in the cradle-to-gate fossil carbon footprint impact of average European sack kraft paper and paper sacks. In only 11 years, from 2007 to 2018, the fossil carbon footprint impact per paper sack has been reduced by 28%, from 118 g CO2e to 85 g CO2e. More information can be found in the latest LCA study.
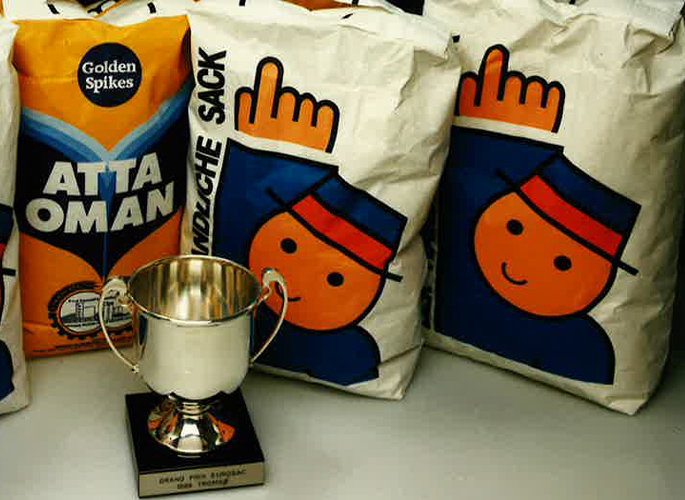
Since around 1980, bleaching technologies have been installed in some kraft pulp mills. The brown sack paper turns white and becomes an attractive advertising medium, also underscoring the hygienic effect. However, brown sack kraft paper continues to be the main raw material for paper sacks.
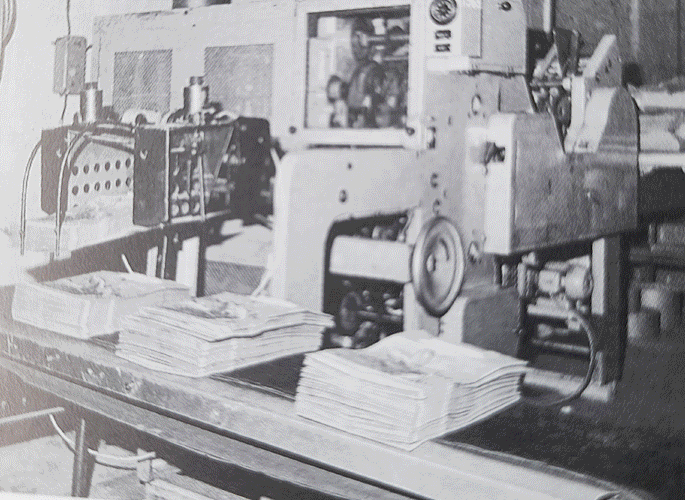
To offer easier and more ergonomic handling of paper sacks, paper sack constructions become more complex. In the late 1970s, paper sacks with handles enter the market. They allow easier carrying of the heavy sacks. Starting around 2000, other convenience features become popular in the paper sack market, such as easy opening, pouring and reclosing systems. There are many different sack constructions available. One example is pet food paper sacks with high-repeatability open-reclose systems thanks to an adhesive label over a pourer spout or a zip fastener with pressure flap. Another easy-opening system works via a funnel-formed effusion opening with which the end user can better dose the filled good. The latest opening system has a handle allowing for comfortable carrying, easy opening and clean emptying at the same time. Sacks with a tircell system (pull tab) on the bottom of the sack enable immediate opening and emptying after pulling the tab. There are also sack constructions serving specific customer needs, for example a paper sack for animal feed with a window made of plastic film that shows the product inside the sack. Dissolvable paper sack for the building industry can be put entirely into the cement mixer, where it breaks up and integrates its components into the concrete or mortar without negatively affecting the quality. Waste is thus eliminated, while cement utilisation and workers’ health and safety are improved. There are also smart sacks with an embedded RFID chip. The identification enables unique allocation of the measured data to an object or retail customer. You can find more examples of special paper sack constructions here.
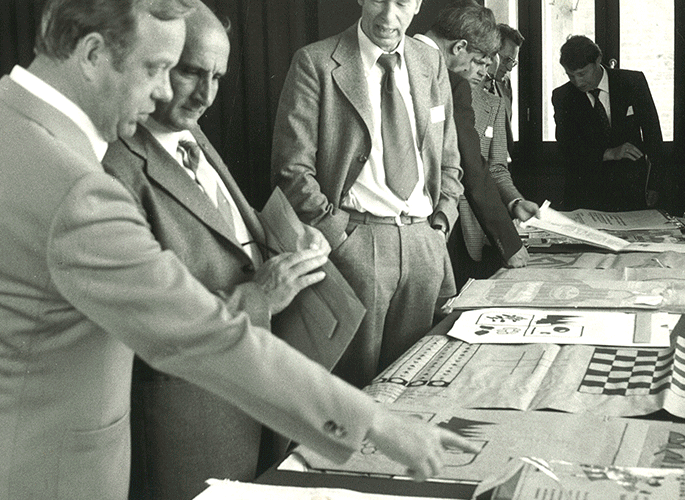
The first EUROSAC Grand Prix Award is held in 1978. It honours the industry’s most recent innovations and shows the innovative strength of the sack kraft paper and paper sack industry. Aside from a pause between 1993 and 2008, the award is presented each year. You can find an overview of the latest winners and entries here.
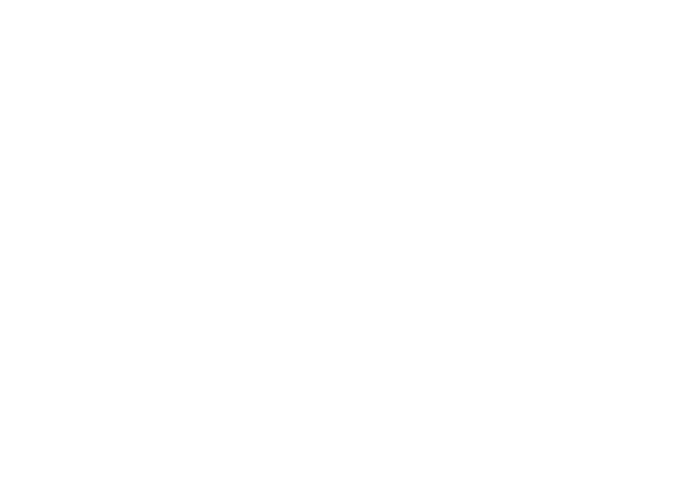
In 1975, the introduction of flexography and the four-colour process revolutionise the printing technology for paper sacks. Flexography evolves the letterpress with high-speed rotary functionality, whereas the four-colour (CMYK) process makes it possible to create the full colour spectrum using only four basic colours for printing. In the 1980s, paper sack manufacturers start using water-based inks which are safe for people and the environment and therefore also allowed for contact with food. In the late 1990s, ink usage is being improved in production, as an example from Gascogne shows: in 1997, they set up an automatic dosing station for ink preparation to avoid losses in inks, followed by a sophisticated ink recycling system that brings rinse residue down to zero and achieves substantial ink savings in 1998. Today, ten-colour printing is the standard in the industry. It uses additional inks beyond the original CMYK ink set for highly realistic quality printing and reduced graininess.
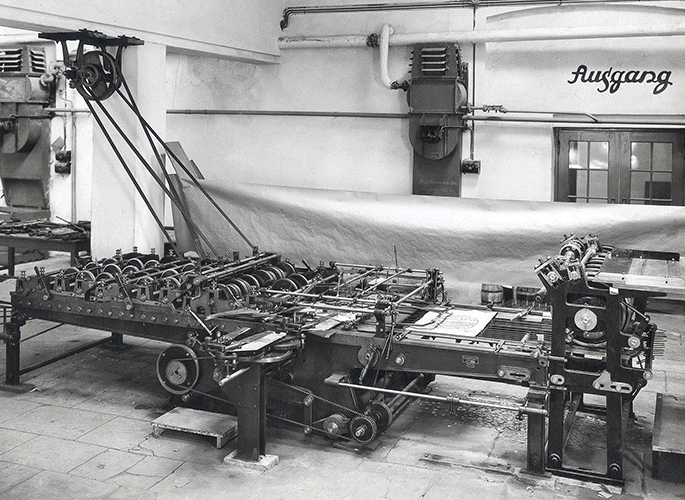
In the 1970s, sealing technology revolutionise paper valve sacks. The hermetic sealing of the valve allows dust-free filling and tight sack closure. The first machines featuring ultrasonic sealing on each (instead of only one) filling spout are released in 1997. Paper sacks featuring a valve had been invented as early as 1902. In 1925, the technology is perfected and sewn valve sacks are enthusiastically welcomed on the market. They eliminate health hazards from cement dust that plagued the industry before that date and enable automation of the filling process. About the same time, folding and gluing machines for pasted valve sacks (bottomers) emerge. In the 1930s, a simpler bottomer concept makes its breakthrough, which permits the folding of both ends at the same time and pioneers the path to the high-speed machines of today.
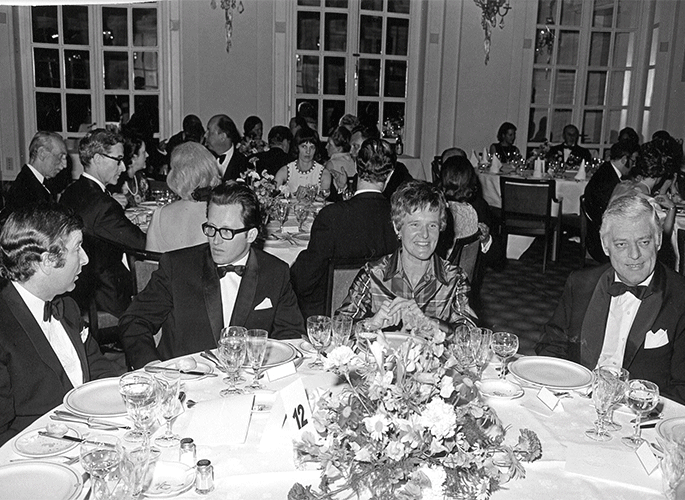
EUROSAC grows: in 1972, 20 years after EUROSAC’s founding, the association has 108 members with 130 plants in 18 countries across Western Europe. By 1995, in addition to ordinary and corresponding membership groups, associate members have also joined the organisation. They are suppliers to the paper sack industry such as manufacturers of paper, machines, adhesives and film, as well as kraft paper manufacturers. The latest addition in the corresponding membership group are carrier bag members that joined in 2017.
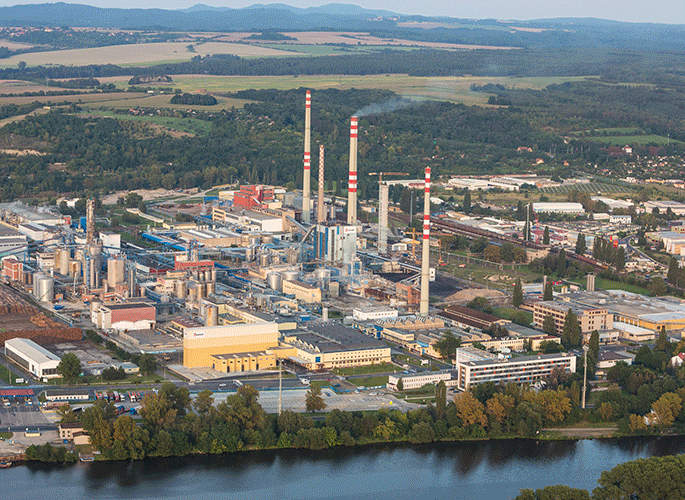
Whether it is environmental aspects, fibre yields, chemicals, inks or glues, the industry has a long track record of saving important resources during production processes. Some examples can be found in the early 1970s. In 1973, Nordic Paper are modernising their Åmotfors mill and building a sedimentation basin for fibre recovery. In the same year, they replace the water treatment at Bäckhammar mill with a circular sedimentation basin with chemical recess. The new purification step has a major positive effect on the nearby lake. A process that permits the environmentally friendly closing of the chemical circuits and the energetic self-sufficiency of the paper mill at large is developed much earlier, in 1929, when a stationary furnace for the reclaiming of chemicals from the pulping process and for utilisation of bio-energy from the spent lye is invented. In 1991, Gascogne installs a new automated boiler for the process of regeneration, reaching a recycling rate of many by-products of 90%, which further contributes to environmental protection. In 2016, the company installs a new biomass-fired boiler. A recent example of closing the loop, from 2020, is the first machine in Europe fully dedicated to recycled kraft paper for shopping bags, by Mondi in Steti mill, Czech Republic.
Thanks to improvements in paper strength, the specific paper consumption – whether due to the numbers of kraft paper sheets used to produce sacks or the reduction of paper grammages – decreases from 253 g per sack in 1969 to 127 g per sack in 2011, resulting in considerable reductions in costs and saving of natural resources. Today, a paper sack for building materials weighs only about 90 g. Whereas in the 1960s, most paper sacks still have five plies, the first one-ply sacks are introduced on the market in the 2000s. Material reductions in barrier films add to the sustainable use of resources. HDPE film was still 23 µm thick when first introduced on the market in 1979, whereas 20 years later it has been reduced to a third of its original thickness: to 8/7 µm.
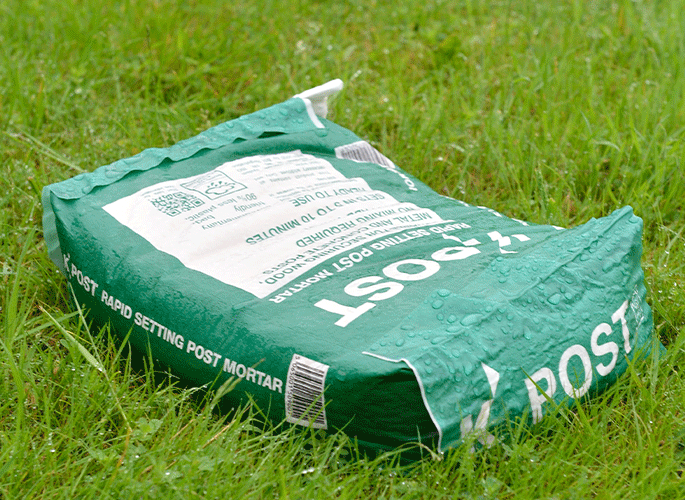
In the 1960s, the combination of paper with plastic to install a barrier is gaining ground. Barriers come into play when the product inside the paper sack needs enhanced protection, e.g. from water vapour, light, oxygen and unwanted aromas. The barriers are used either as inner ply, outer ply or coating. Depending on the requested function, different materials can be chosen. In 1969, PE-film inserting units are developed for paper sack machines. Liners that were previously mostly inserted manually can now be inserted with speeds of 100 per minute. In 1979, HDPE (high-density polyethylene) is first introduced on the market as a barrier film for valve bags, and tubular film for open-mouth bags. HDPE has strong barrier properties regarding water vapour and is used for products that require special moisture protection. Its usage clears the way for the water-repellent paper sacks that enter the market in 2015. Some examples are HYBRIDPRO, a paper sack with PE as the outer ply which maintains the paper sack properties in rain and SPLASHBAG, a water-repellent paper sack without any coating that withstands rain for up to six hours, both by Mondi. SAFEdy Showerproof by dy-pack provides protection against moisture, air and gas penetration and RainSafe by BillerudKorsnäs withstands up to four hours of rain according to EN ISO 2875.
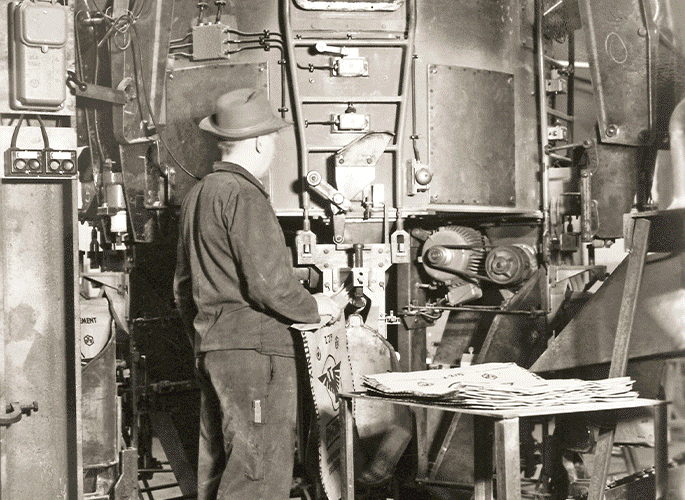
In the 1960s, cement demand grows worldwide. As a result, greater demand for packing systems with higher production rates arises. The first ROTO-PACKER® by HAVER & BOECKER leaves the factory – an innovative solution based on a rotating filling machine for powdery products. It has three filling spouts and reaches filling speeds of 900 sacks per hour. Efficiency is further enhanced with a breakthrough in automation in 1975 via the first bag applicator for rotating machines. Step by step, the system is supplemented. Automatic weight checking leads to unprecedent weight accuracy and automatic rejection brings about comprehensive quality assurance. In 2015, an intelligent filling machine with self-optimising aeration adjustments for decreasing the amount of air during the filling process is introduced on the market. Since 2020, the filling machines have been able to monitor, control, analyse and optimise the filling processes digitally. This leads to a reduction in downtimes and costs and contributes to a further increase in efficiency, especially in service and maintenance. The most advanced and fully automatic packaging line for industrial goods of our time, with a maximum of 16 filling spouts, reaches filling speeds of up to 6,000 sacks per hour.
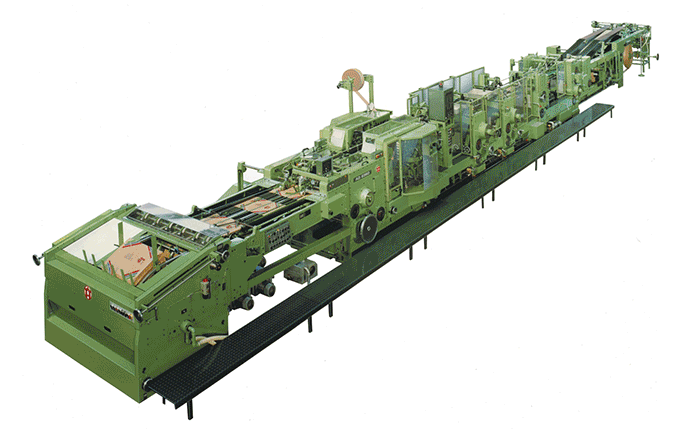
In the 19th century, the first industrial paper sacks are produced. In the 1950s, the growing number of filling goods requires the development of different sack constructions. In 1968, W&H presents a new paper sack machine: the universal bottomer AD 2360, an advanced folding and pasting machine for multiwall paper valve sacks. It is the most successful bottomer ever and becomes the workhorse of the paper sack industry worldwide. About 20 years later, in 1982, the AD 2366 NC follows, featuring an electronically controlled, automatic size set-up and change-over system, increasing productivity significantly from 160 sacks per minute in 1975 to 250 sacks per minute. Starting in 2008, W&H develops a digital (nozzle) glue application system that revolutionises pasting technology, resulting in improved productivity and in drier, better-looking sacks. This first digital bottomer allows a fast response to specific customer needs and a higher level of efficiency through an ideal synthesis of extensive automation, minimum maintenance requirements and high speeds of 360 sacks per minute. With a clear focus on industry-leading technology and innovation, in 2021, paper sack production is brought to a new level with automatic roll changes in the tuber and improved automation in the bottomer leading to an output of 400 sacks per minute – a new milestone in the history of paper sacks.
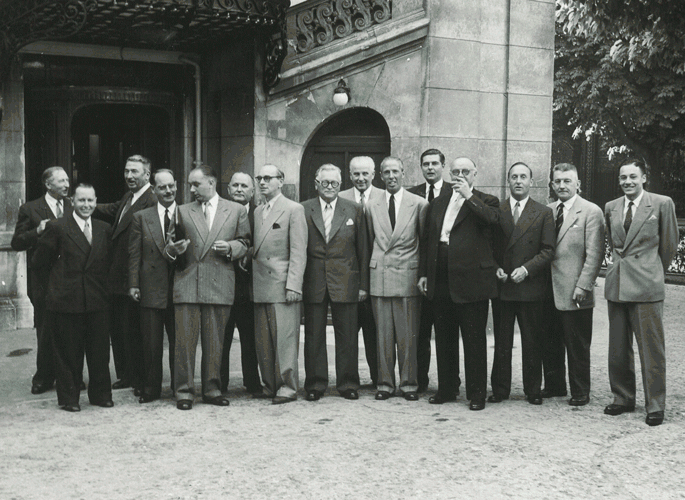
The European federation of multiwall paper sack manufacturers, EUROSAC, is founded in June 1952 by manufacturers from Germany, Belgium, France and the Netherlands. They start out with two membership groups: paper sack manufacturers from Europe (ordinary) and worldwide (corresponding). They are convinced that this can provide a secure basis for the future of all in the same industry, favourable to both business and friendly relations. In November, the first EUROSAC congress takes place in Hamburg, Germany, with as many as 12 countries taking part. Since this date, the congress has been held annually and unites all members in a general assembly. Only ten years later, at the congress in Oslo, Norway, it is announced that the production of the association’s members topped by 30% that of the USA and Canada combined.
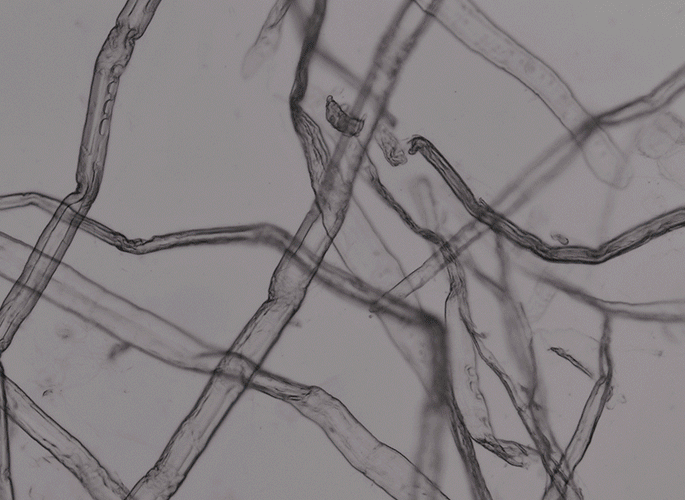
As early as 1940, the sack kraft paper industry starts efforts to strengthen the fibre structure of the paper by using melamine-formaldehyde resins for the first time. This results in wet-strength sack papers which maintain their strength even when wet. In 1947, a new process for micro-creping of paper (fibre compression) enhances paper strength even further. It leads to a smooth, easily printable paper featuring improved elasticity, which, aside from tensile strength, is the decisive factor for the sacks’ ability to withstand shocks, for example when being filled at high speeds. Known as CLUPAK-paper, it makes the production of sacks from lower basis weight papers or sacks with fewer plies than before possible. The continuous development of fibre processing technology as well as process control on the paper machine results in significantly improved mechanical properties of sack papers. This is improved by 45% in a time span of 20 years. In 2001, the strongest paper in the world from Mondi enters the Guinness book of records. It can carry a 4.2-tonne container on a single sheet. Two years later, Mondi unofficially breaks its own record by parking and lifting a 9.8-tonne locomotive on a single sheet.
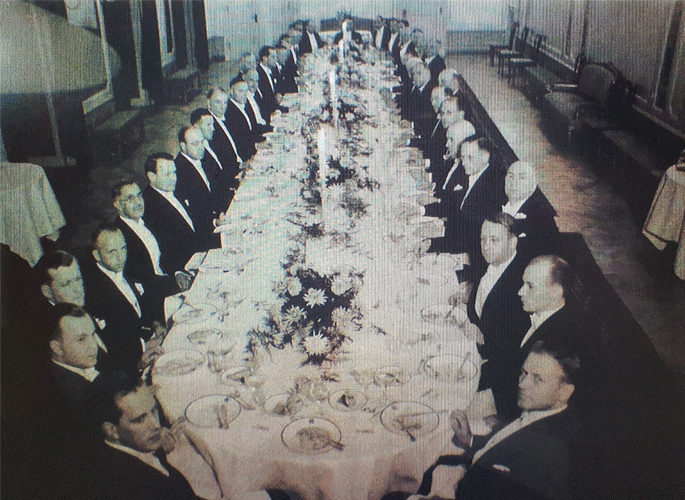
Scankraft is formed in 1932 to represent the Scandinavian kraft paper manufacturers. Its main purpose is to act as a coalition for achieving price stability in a time when the gold standard is abandoned, and prices decline sharply. The efforts are seen quite positively by customers as the organisation always tries to reach an acceptable lowest limit. 30 years later, Scankraft is succeeding in its goal and the volume of kraft paper produced increases from 150,000 tonnes in 1932 to 1 million tonnes in 1962.